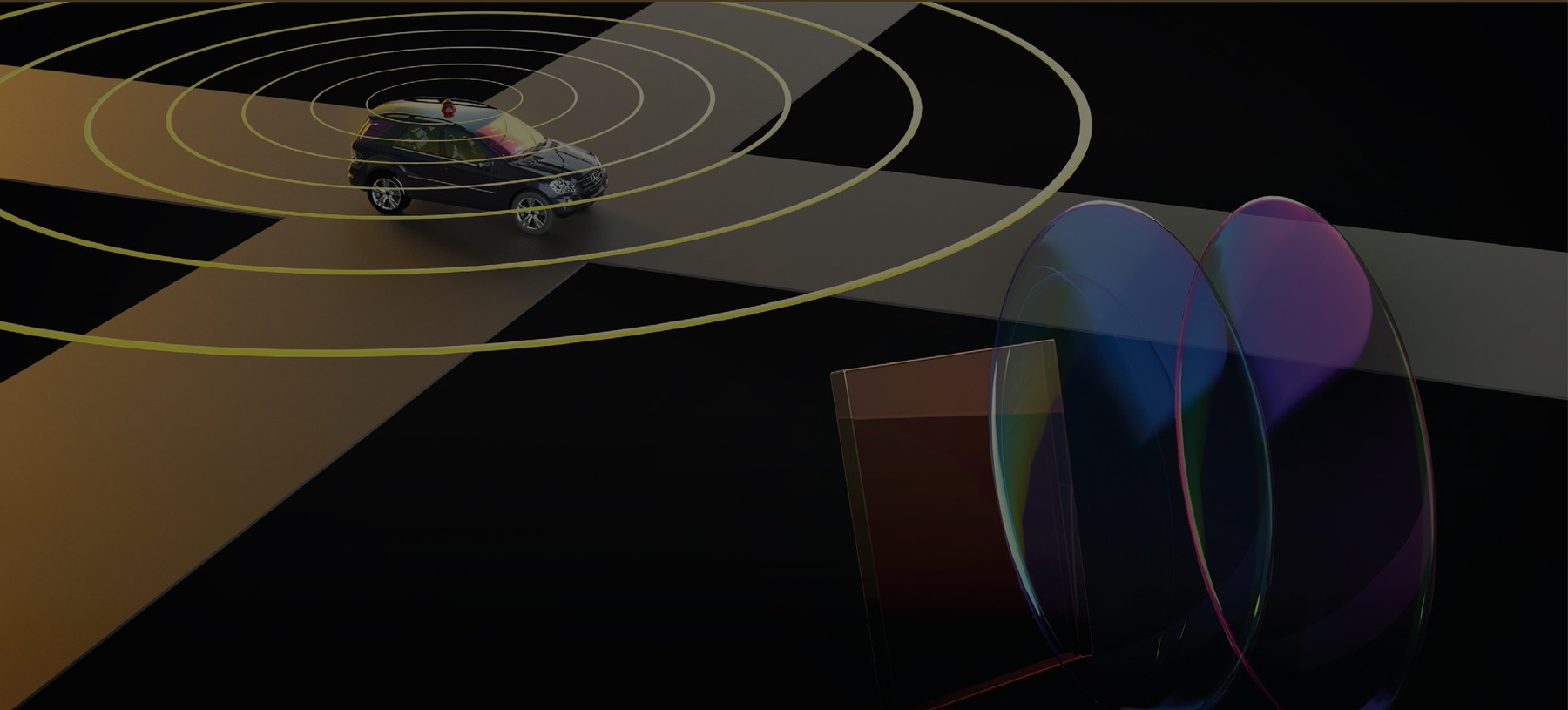
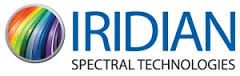
LiDAR, short for light detection and ranging, uses pulsed lasers to accurately calculate distances as well as correctly detect the size and shape of objects. The high resolution of the information — LiDAR can resolve to a few centimeters from more than 100 meters away — and the ability to create accurate model three-dimensional images have made the technology critical in many applications. Some uses include autonomous vehicles and automobile crash avoidance, surveying, environment, construction, agriculture, oil and gas exploration, and pollution modeling.
The applications use lasers that emit light of specific wavelength and standard silicon detectors that typically respond to anything from 300 nanometers to 1,200 nanometers. High-quality optical filters are part of the design, so the detectors, as much as possible, see only the reflected laser light. Integrating filters into a design can be challenging, which is why learning to correctly choose and incorporate filters can save a company time, money, and frustration.
By obtaining informed advice at the outset and making some easily accommodated changes to the design process, companies can save time and money while achieving their goals.
How LiDAR Works
LiDAR is similar to radar. Both measure distances by emitting a signal — laser light for LiDAR and high-frequency radio transmissions for radar — that reflects off a distant object back to the system. Electronic circuity measures the time between sending and receiving the signal and calculates the implied distance.
A system will send the laser pulses and measure the time they take to reach the object in question and travel back after reflection, either by directly clocking the time or by noting a phase shift in the returned light and calculating time from that.
A LiDAR system rapidly pulses a laser of specific wavelength, whether 532, 905, 1064, 1054, or 1550 nanometers. Different wavelengths lend themselves to specific applications. For example, the 905-nanometer wavelength has become popular in autonomous vehicles, while the 532-nanometer is a green laser that works well under water.
Although there are custom gas-based detectors that can work with specific wavelengths, LiDAR equipment designers typically use silicon-based broadband detectors that react to wavelengths between 300 and 1,200 nanometers. The reason for the choice is cost, as such devices are relatively inexpensive and, therefore, easy on a project’s budget.
Unfortunately, the broadband nature of the detectors creates a problem. A unit will respond to not only the laser in question but many other light wavelengths and sources. To adapt a broadband device to a narrow set of wavelengths, LiDAR applications require filters to eliminate extraneous wavelengths and focus on the specific laser wavelengths in use. The equipment can then avoid false readings and reduce unnecessary information for faster and more effective analysis.
Filter Considerations
The filters used in a LiDAR system are, in concept, no different from a pair of sunglasses. The filter manufacturer coats a transparent base, called the substrate, with thin films of appropriate substances that, in theory, allow the laser’s light wavelength to pass through while blocking others. In practice, there are multiple working characteristics to consider:
- Highly transmissive at desired wavelengths — The more light at the laser’s wavelength the detector can collect, the more sensitive it can be. Because all the light will pass through the filter, a high degree of transmission at the specific wavelength is desirable.
- Deep and broad blocking — As much as the filter needs to pass light at the laser’s wavelength, it also should block as much other light as possible. Otherwise, the sensor would detect the additional light and potentially give false readings.
- Field of view — The light reflected from a LiDAR system may come back directly to the detector. However, for many applications, including for autonomous vehicles, the light may be received at the detector over a wide angle range. The physics of multi-layer interference films implies that the spectral shape of the filter for light passing through at a higher angle of incidence will shift to a shorter wavelength. For example, a filter intended to transmit 905 nanometers might shift transmission below 900 nm for light incident at a large angle. This may require design of a wider transmission band to account for the angle shift for a wide field of view, which can have negative consequences for signal-to-noise ratio.
- Surface — Defects on an optical surface are important to address, but only in the context of the light passing through. A defect that might interfere with light in the visual spectrum might not matter in the longer wavelengths used in LiDAR. Unnecessary correction will drive up costs.
- Operating conditions — LiDAR systems do their work outside of a lab temperature. Temperature and humidity can affect how well coatings perform. A LiDAR filter will have to work in whatever environment it is placed.
- Signal-to-noise ratio — As is true with any communications system, there is an inherent degree of background noise. The filter needs a high enough signal-to-noise ratio to pass enough actual signal content through to the detector. This is achieved through the combination of high and narrow transmission with deep and broad blocking.
- Size — The larger the filter, the more difficult and costly it is to manufacture.
- Structure considerations — Manufacturers make filters in layers. The choice of layer materials and methods of depositing them on the substrate affect all of the above characteristics.
All the characteristics represent a set of trade-offs to make. The wider the angle of view, the greater the set of wavelengths the detector will see, reducing the range of blocking. The smaller the filter size, the less light that can pass through, although the designer gains a cost reduction. A coating that improves the signal-to-noise ratio might not perform well in the conditions under which the LiDAR system will work.
The trade-offs provide a range of unintended consequences to design choices. Focus overly on one aspect, like wavelength selectivity, and the resulting product might be weak in another area — field of view, for example. Working with a filter vendor can aid designers and engineers in developing applications, recognizing problems before they happen.
Working With The Filter Vendor
To avoid problems, the best time to start working with a vendor’s filter experts is early in the project for the maximum flexibility.
Approach the process with an eye to real-world conditions and solutions rather than what sounds best in theory that could drive up costs. For example, over-specification can be a major blockade to faster and better results. A wish list of tighter specifications can make it more difficult to construct a filter that meets the requested characteristics necessary for actual use.
One example is filter size, where it may be considerably more expensive to buy large filters and cut them down to the needed size rather than requesting the construction of small individual filters. Another example is wavelength blocking. If light is outside a detector’s ability to react, there is no need for the filter to keep it from reaching the detector. Changing the size and placement of a filter in the optical path can affect how the entire device works and might improve performance while reducing costs.
Stay open to different solutions. The goal is to obtain the wanted results from a new device while balancing technical and business needs, not to prioritize design choices that may have become habitual.
The most important lesson is to treat a filter vendor as a collaborator and partner. The experts in filter design and manufacturing can raise important questions based on experience and knowledge that might greatly help bring an application into reality.
For more information on LiDAR and filters, please see https://iridian.com.cn/application-areas/ optical-filters-for-lidar-laser-sensors/ and https://iridian.com.cn/application-areas/optical-filters- lidar-applications/
Iridian Spectral Technologies Ltd (Iridian) is a diversified optical filter manufacturer that is an international leader in filter design and manufacture especially for application in the fields of fiber optic communications, optical spectroscopy, 3D entertainment, and in aerospace. Iridian is a global supplier with distributors in many countries.